With so many moving parts, both literal and figurative, operating a warehouse comes with all manner of different challenges. Without the appropriate measures and approaches in place, costs can soon start to spiral. Alongside vast amounts of competition and an unstable economy, mounting expenses can do some real damage to your profits if certain precautions aren’t taken.
Managing your warehouse and its operations can be the difference-maker, keeping costs down and ensuring that everything else runs like clockwork. And much of this efficiency lies in making the most of your warehouse’s available space.
Below, we’ll show how optimising warehouse space can help improve its cost-effectiveness through a series of powerful strategies. Let’s get started…
Optimise Your Storage
The space and layout of your warehouse play an important role in how it operates, but it’s something some managers might end up overlooking. With land costs greatly contributing to overall expenses, however, rethinking how you use your space can help your facility become more cost-effective. In fact, you can store more in less when you know what you’re doing.
In a warehouse where space hasn’t been optimised, you’ll likely be faced with challenges to flexibility, affordability and access. A fully optimised warehouse, on the other hand, can improve traffic flow, reduce loss of stock and keep staff productive. When these positives combine, you’ll be putting yourself in a position to decrease costs, increase profits and keep customers happy.
If setting up a second location or expanding your existing site is out of the question, then you should aim to optimise the space you do have. Try building your storage upward, for example. Elsewhere, you can minimise the existing distance between your current aisles by creating alternating one-way aisles. Doing so minimises travel time from aisle to aisle, reduces equipment collisions and lets equipment handlers access both sides of the aisle when picking or stowing.
Prevent theft and damage
Whether it’s theft, damage or simply misplacing items, stock issues can wreak havoc on your business’ costs and profits.
Problems with damage and misplacement can be easily rectified. If unintentional damage is a recurrent issue, then educating and training your team on the proper packaging procedures can get them up to speed. Meanwhile, product misplacement can be combated through proper control systems, such as MWS, RF, RFID and CDP.
Theft might be a lot trickier to deal with. Identifying if it’s taking place at all can be a challenge in itself.
There are a few warning signs to watch out for which can help, however. As well as the staff rumour mill, use your business or ERP software to look out for things such as discrepancies between stock levels and sales records, fluctuating sales when specific staff are on duty, missing invoices and stock always appearing at exits or loading bays.
You can prevent theft by encouraging staff to be more vigilant, controlling access points through a key card system, and installing security cameras and alarms. If your warehouse does not run 24/7, then you might want to consider using a rotational guard system during off-hours.
You can also employ your ERP system to trace back stock activity to the individual user by looking at the audit trail history on the system to enforce accountability and transparency.
Start cross-docking
Think of cross-docking as a way of cutting out the middleman. Through cross-docking, product is transferred from the supplier directly to the customer, slashing costs across multiple points within your warehouse, including product management, storage, handling and labour.
In a cross-docking environment, superfluous pathways are cut away, leaving a lean and trim process that expedites shipping to the customer. So how do they work?
In such terminals, inbound products arrive through delivery trucks, where they’re allocated to a receiving dock on one side. Upon docking, the trucks’ contents can then be moved to the other end of the cross-dock, using forklifts, conveyor belts or pallet trucks. Once the outbound transportation has been loaded, the products can then be delivered to customers.
Optimise the picking process
An inadequate picking process can sap time and money. But one that’s designed with speed and accuracy at its core can help reduce the costs that occur through poor practices. Make your warehouse more reliable and cost-effective through:
- Prioritising priority and VIP orders first
- Keeping items that are often selected together in close proximity
- Arranging items in batches or clusters so that staff can make more than one collection at a time
- Ensuring stock is clearly labelled
- Storing inventory in the appropriate storage, whether that’s in a bin or on pallets
- Avoiding vertical picking where possible
- Storing slow-moving stock vertically
Leverage demand forecasting
It might seem prudent, but a warehouse should avoid being overstocked. Not only is it expensive to purchase up front, but it’ll cost you to store the stock too. On the other hand, under-stocking can also be an issue if you have to deal with long lead times just to receive the stock itself.
Demand forecasting is one way of ensuring your stock levels are managed more effectively. Through demand forecasting, ascertaining the peaks and valleys in future demand lets your warehouse replenish the stock in good time and keep control over its capacity.
By looking at historical sales patterns to seasonal events in the retail calendar, you can carry out detailed, fine-tuned analysis of certain variables, equipping you with data and insights that let you plan out your stock requirements days and even months in advance.
ERP systems offer in-built, advanced replenishment functionality that takes the guesswork and administration out of forecasting. They streamline purchase processing by incorporating your historical sales data that has been augmented to remove any anomalies and your business rules related to maximum and minimum stock levels, forecast peaks etc. to present your team with robust replenishment orders.
Enhance your slotting
Slotting is essentially the process of having the right product in the right place at the right time. By analysing inventory data in order to better categorise and organise it, it’s possible to boost the productivity, efficiency and, ultimately, efficiency of your operations.
In optimising your slotting, things like picking trends and warehouse trends can pinpoint and create your facility’s “golden zone” – the area that’s most accessible and stores your fastest-moving items. By storing larger, heavier and slower-moving inventory away from this area, your staff can pick faster and more accurately, and you can lower your overheads. With order picking making up some of your warehouse’s biggest costs, optimising your slotting can help to slash these expenses greatly. You should regularly use your ERP software to run fast- and slow-moving stock reports to ensure your ‘golden zone’ is constantly optimised.
Invest in a warehouse management system
Whether you opt for a warehouse management system (WMS) or an ERP with a strong WMS component (such as Intact iQ), the right technology can help improve your efficiency by streamlining existing processes, such as suggesting optimal forecasts, picking routes, reducing paper wastage and minimising picking discrepancies caused by human error. A WMS can also help with the increased loss of inventory control that comes with cross-docking solutions and will help you spot any incidences of theft.
Through its ability to keep the most critical information close to hand, a WMS can alert you to everything from issues with stock to incoming trends, allowing you to save time and make important decisions in an instant.
Increasing your warehouse space through ERP software can give your operations room to breathe. Looking to free up your facility and improve your day-to-day processes? Our products can help with that, and then some. For more information, get in touch with our expert team.
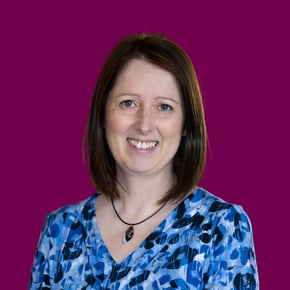