What Are the Different Types of Inventory and How Can You Best Manage Yours?
Inventory is, without question, the most high-value asset a business can acquire. From raw materials to finished goods, stock comes in many forms, and understanding the different types is critical in maintaining efficient inventory management practices.
Businesses in every sector rely on different types of inventory goods. Products, materials, components, and even cleaning products and packaging, are all classed as controllable physical assets within a modern inventory stream – and understanding how to manage them all is a critical part of day-to-day operations.
In this guide, we’re taking a look at different types of inventory, before offering a handful of essential tips on effective stock management.
Types of Inventory Explained
Inventory takes many forms and, as technological advancements continue to transform logistics and infrastructure, there are almost certain to be new types of stock in the future. Here, we take a look at the 10 primary inventory types – from raw materials to safety stock.
Raw Materials
Accrued at the beginning of the inventory management cycle; raw materials are items used to manufacture and produce final products. A business may purchase raw materials to manufacture or assemble its products or else sell them to third-party organisations who then transform them into a finished product.
Raw materials are among the most essential stock items in an inventory chain. They dictate manufacturing rates and productivity, so effective and timely procurement is essential. Businesses should use an appropriate inventory management platform to track, manage and store its raw materials inventory.
Work-in-Progress (WIP)
Work-in-progress inventory refers to goods that, while no longer in their raw-material state, aren’t yet complete and ready for sale. Examples of this include a car that hasn’t yet had its engine installed, or a scented candle without a wick.
WIP stock is easy to overlook because it’s often part of a complex production cycle, whereby goods are moving through various manufacturing stages. A modern ERP solution can help monitor such stock, with real-time tracking and smart inventory management controls.
Finished Goods
As the name implies, finished goods refers to stock that is complete and ready for sale. This type of inventory may have been manufactured by the business itself (from raw materials and WIP stock) or it may have been purchased as a whole and complete product.
Finished goods are an important inventory item within the supply chain cycle. That’s because they represent the crossover point between manufacturing supply and retail supply. Many retailers, therefore, will only need to manage their inventory from this point.
Because ‘finished goods’ is such a broad inventory category, many businesses break things down further into useful subcategories; this helps with prioritising and managing stock. Five additional categories are used in relation to finished goods, including
- Ready for Sale – stock that can be picked, shipped or sold at a minute’s notice is known as ‘ready for sale’ or ‘available inventory’.
- Allocated – allocated inventory is that which has been sold to a customer and put on a sales order, so should be put aside and marked as such. Accurate and timely inventory management is critical when handling allocated stock.
- In-transit – in-transit inventory refers to unsold stock that is on the road, either between warehouses or on route from the supplier.
- Seasonal – seasonal inventory is that which is made available in anticipation of specific trading periods, including public holidays and sales events.
- Safety (Buffer) – safety, buffer or surplus stock refers to inventory items procured to safeguard against sudden upturns in demand. It helps to avoid sold-outs and meet customer expectations.
Maintenance, Repair and Operations (MRO)
Maintenance, repair and operations (MRO) goods are those which are used as part of a manufacturing supply chain. They’re the ‘essential’ items that a business needs as part of its day-to-day production operations, including things such as PPE and safety equipment, parts and manufacturing equipment, cleaning supplies and batteries.
Many businesses overlook MRO stock as part of their inventory management strategy. But it’s important to remember that such goods may play a vital role in everyday operations, aiding personnel in all aspects of the manufacturing cycle. Such items will also need to be stored, logged and ordered in an effective, timely way so as to avoid overstocking or wastage.
Packing Materials
Packing materials inventory refers to all the items required as part of logistics, warehousing and delivery operations. It includes goods and materials that are used for both shipping items to customers and as a means of protecting stock in the warehouse – think boxes, packaging, paper, bags and bubble wrap.
As with MRO stock, packing materials are regularly left out of a formal inventory management strategy. But, just as with PPE and cleaning goods, packing materials are an essential part of day-to-day operations and need to be accounted for – particularly if you want fiscal reports, COGS and turnover to be as accurate as possible.
Essential Tips for Effective Inventory Management
Managing inventory may seem straightforward. But with lots of moving parts and a cashflow to maintain, it’s a business function that requires commitment, investment and a considered approach.
Below, we share five essential tips for managing an inventory effectively. These practices can be applied to all types of inventories, whether that’s raw materials, finished goods or MRO.
- Prioritise – some stock will fly off shelves while other items sell more slowly. Prioritising your inventory will help you order the materials and goods you need to retain cash fluidity. Many firms use an ABC approach when prioritising stock, with ‘A’ representing stock that needs to be reordered more frequently and ‘C’ items with a longer turnaround time.
- Track – tracking product information throughout a supply chain is fundamental to effective inventory management. ERP software can facilitate accurate ‘batch’ tracking, which is useful for grouping inventory items by SKU, barcode, lot number and country of origin.
- Audit – regularly auditing your inventory is a powerful way to avoid common management issues such as under or overstocking or product tracking inaccuracies. Performing regular stock checks is essential throughout the supply chain, reducing the likelihood of problems and backlogs further down the line.
- Analyse supply chain performance – however tightly you control your inventory, inefficiencies, delays or inaccuracies within the wider supply chain can have a negative impact on day-to-day operations. That’s why it’s critical to periodically analyse and review the performance of your supply chain; what works and what doesn’t. And do any of your suppliers regularly cause problems (late deliveries, missing items) that have a knock-on effect within your organisation?
- Invest in the right inventory management platform – effective and accurate inventory management relies on having the right tools and processes in place to control stock efficiently. And while it is possible to manage inventory manually, technology is your friend in this regard. A modern ERP system can make light work of managing even the most complex inventory infrastructure, with batch tracking, smart stock control and other useful functionality facilitating competent and accurate management.
Have you enjoyed this guide? Perhaps it’s inspired you to review your own inventory and stock management processes? At Intact, we believe that with the right tools and processes, any business can improve and enhance how it controls its physical assets. To learn about our powerful, future-fit business management solutions, visit the homepage or get in touch.
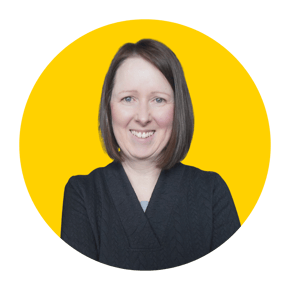